Power Plant Industry
Revolutionizing Maintenance: Industrial Ultrasonic Cleaning in Power Plants
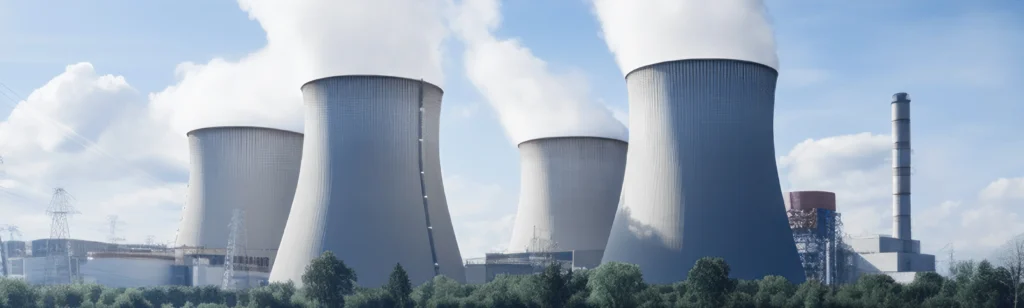
A modern technique that can fully transform power plant industry maintenance procedures is industrial ultrasonic cleaning, which enhances power plant efficiency by precisely removing contaminants, reducing downtime, preventing corrosion, and promoting environmental sustainability.
Power plants traditionally used manual or mechanical techniques for cleaning components before the introduction of ultrasonic cleaning. Some of the common cleaning methods employed in the power plant industry include:
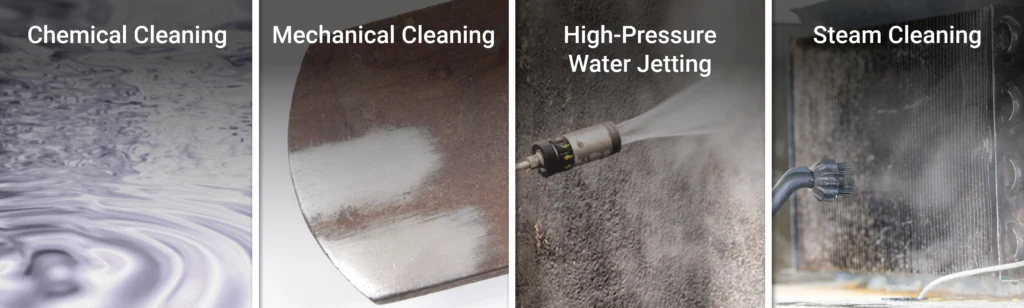
- Chemical Cleaning: Chemical cleaning involves specialized cleaning agents or solvents to dissolve or break down contaminants on surfaces. Moreover, it is effective for removing certain types of deposits and scale.
- Mechanical Cleaning: Methods, such as brushing, scraping, or blasting with abrasives, physically remove deposits, rust, or scale from surfaces. While effective, these methods might not reach all intricate areas.
- High-Pressure Water Jetting: Water jetting at high pressures was used to dislodge and remove deposits from surfaces. Additionally, this method is effective for cleaning external surfaces and some internal components.
- Steam Cleaning: Steam cleaning involves the use of high-temperature steam to loosen and remove contaminants. It is suitable for certain applications but may not be as effective in intricate or hard-to-reach areas.
Applications in the Power Plant Industry
In the power plant industry, ultrasonic cleaners work by using high-frequency sound waves to produce small bubbles in a cleaning solution, which effectively cleans power plant components like pipes, valves, and fittings. When these bubbles come into contact with surfaces, they burst, producing powerful shock waves that push impurities like grease, grime, and scale out of the delicate shapes of the parts. By reaching places that are hard to reach for conventional cleaning techniques, the cavitation process ensures complete and effective removal of impurities, improving the functionality and lifespan of power plant equipment.
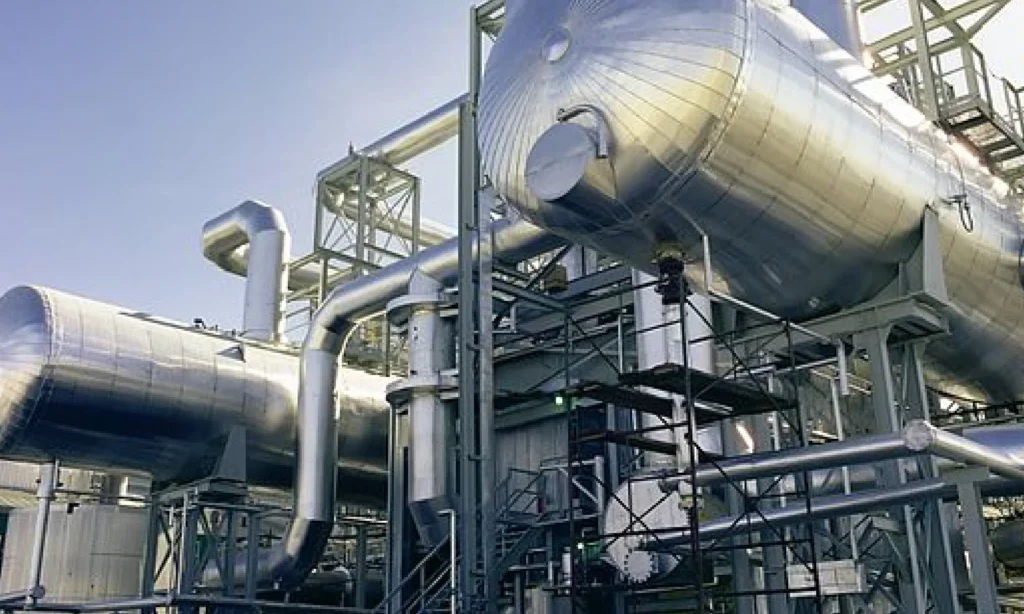
Heat Exchangers: Ultrasonic cleaners prove highly effective in maintaining the optimal performance of heat exchanger tubes, because it ensures seamless operation and extending the lifespan of the heat exchange system by thoroughly eliminating scale, deposits, and fouling.
Turbine Blades: Enhancing the aerodynamics and efficiency of turbine blades through regular cleaning plays a pivotal role in boosting power generation. This proactive approach not only optimizes performance but also extends the operational lifespan of the turbine, ensuring sustained and increased power output.
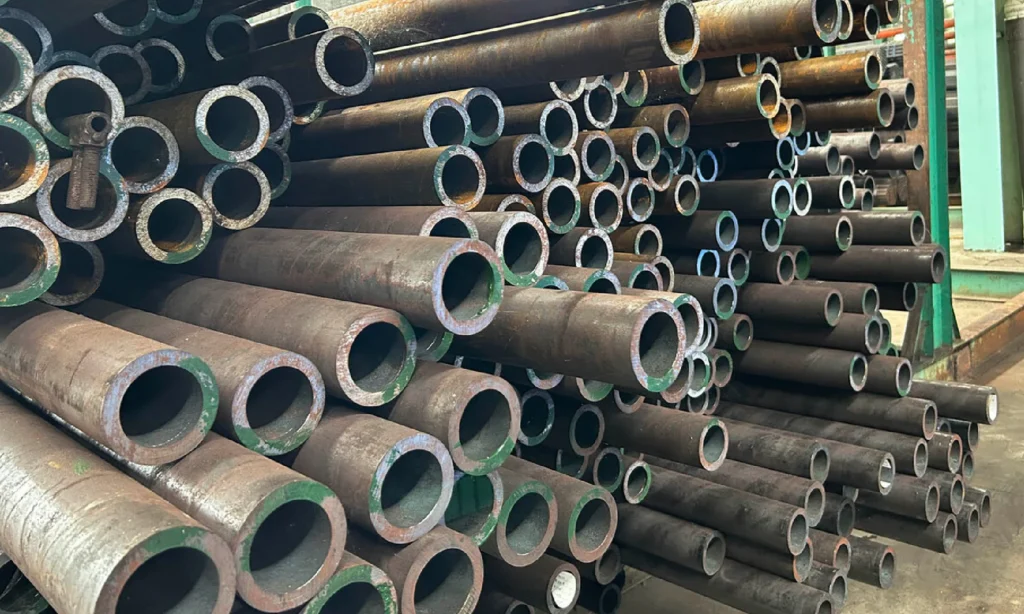
Boiler Tubes: Enhancing energy transfer and reducing maintenance demands, ultrasonic cleaning proves effective in eliminating scale and corrosion from boiler tubes. This meticulous cleaning process not only optimizes boiler performance but also contributes to prolonged operational efficiency.
Piping Systems: Ensuring unimpeded fluid flow is vital, and this involves the thorough removal of rust, scale, and debris from pipes, valves, and fittings. This proactive maintenance not only prevents potential blockages but also enhances the overall efficiency and longevity of the system.
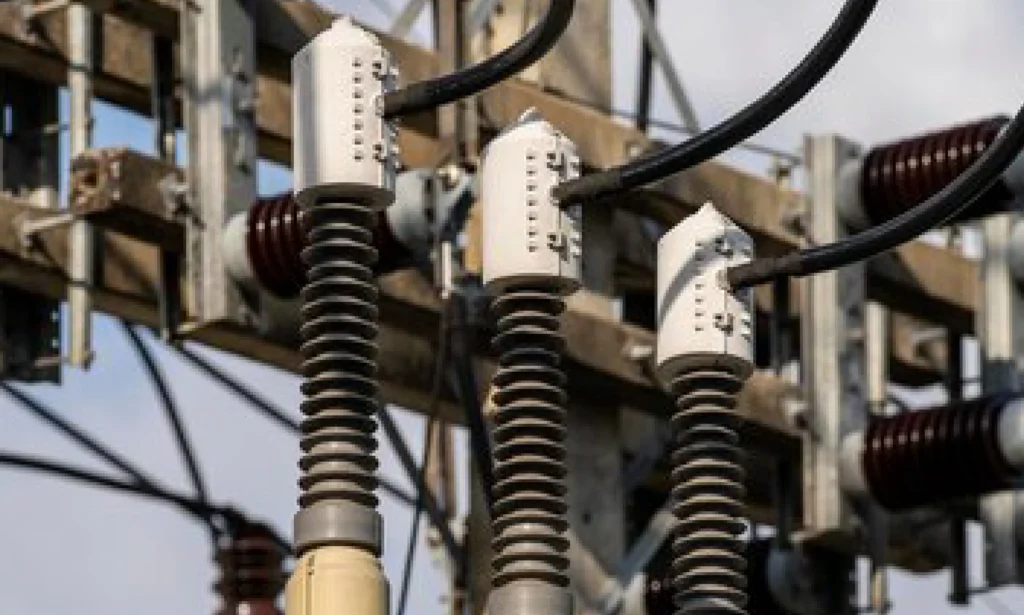
Overview of Contaminants Affecting Power Plant Components: Causes, Effects, and Solutions
Scale and Deposits:
- Causes: Formation due to the precipitation of minerals from water used in cooling systems.
- Effects: Reduced heat transfer efficiency, increased energy consumption, and potential equipment damage.
- Solutions: Water treatment programs, regular cleaning, and use of scale inhibitors.
Corrosion:
- Causes: Exposure to corrosive elements in water, gases, or chemicals.
- Effects: Structural damage, leaks, and reduced component lifespan.
- Solutions: Corrosion-resistant materials, protective coatings, and proper water treatment.
Dirt and Debris:
- Causes: Ingress of particles from the environment or within the system.
- Effects: Reduced efficiency, increased wear, and potential blockages.
- Solutions: Filtration systems, regular maintenance, and proper sealing of equipment.
Oil and Grease:
- Causes: Leaks, improper lubrication, or contamination during maintenance.
- Effects: Reduced efficiency, increased friction, and potential damage to moving parts.
- Solutions: Proper maintenance practices, oil separation systems, and regular equipment inspections.
Microbiological Growth:
- Causes: Presence of bacteria, algae, or fungi in water systems.
- Effects: Biofilm formation, corrosion, and reduced heat transfer efficiency.
- Solutions: Biocides, regular cleaning, and water treatment to control microbial growth.
Foreign Material in Fuel:
- Causes: Impurities in fuel sources.
- Effects: Combustion issues, equipment fouling, and increased emissions.
- Solutions: Fuel filtration, quality control measures, and using cleaner fuel sources.
Advantages of Using Industrial Ultrasonic Cleaners in the Power Plant Industry
- Efficiency: When components are clean, they work optimally, resulting in improved energy transfer and overall plant efficiency.
- Reliability: Thorough cleaning decreases the chance of corrosion, clogs, and mechanical breakdowns, guaranteeing that power is generated continuously.
- Cost Savings: Because cleaned components require less regular maintenance and have fewer unexpected breaks, downtime and associated expenses are reduced.
- Safety: Electrical failures and risks are reduced when electrical components are cleaned.
- Environmental Impact: Ultrasonic cleaning can help to limit the use of harsh chemicals, making for a more ecologically friendly cleaning method.
In conclusion, the integration of industrial ultrasonic cleaning technology has proven to be a highly effective and efficient solution for addressing contamination challenges in the power plant industry. Ultrasonic cleaning is a non-invasive, environmentally friendly method that reduces harsh chemicals and manual labor, making it cost-effective and sustainable in power plant operations. Additionally, power plants can lessen the negative effects of impurities like corrosion, microbial development, and foreign materials in fuel by including industrial ultrasonic cleaning into standard maintenance procedures. In the end, this technology contributes to the long-term sustainability and peak performance of the power generation sector by guaranteeing the dependability, safety, and efficiency of power plant operations.
For other Sonixtek news and updates, follow the Sonixtek Facebook Page.