Plastic Industry
Revolutionizing Cleaning in the Plastic Industry
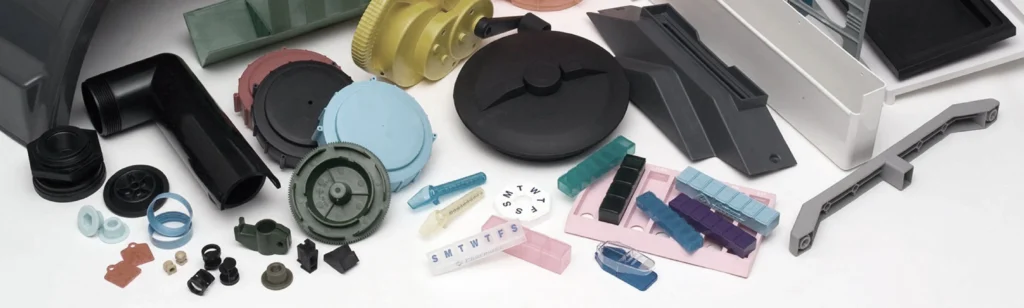
The plastic industry is a key player in many industries, making a substantial contribution to production and manufacturing processes. The efficiency and quality of plastic components are increasingly dependent on the usage of ultrasonic cleaning technologies in industrial applications.
Manufacturers widely use plastics, known for their economic efficiency and adaptability, in producing a diverse range of goods, including complex automotive and electrical component parts, as well as packaging materials. These plastic components frequently pick up contaminants, residues, or mold release agents during the numerous manufacturing processes they go through, which can have an impact on how well they work and look.
The plastic industry uses industrial ultrasonic cleaning, a very effective technique that uses high-frequency sound waves to produce small bubbles in a cleaning solution. When these bubbles explode, they produce powerful shock waves that efficiently clean impurities from plastic surfaces. Because ultrasonic cleaning is harmless, it is perfect for complicated and fragile plastic parts that are difficult to clean with conventional methods.
Applications in the Plastic Industry:
In the plastic industry, ultrasonic cleaners have become popular to clean plastic components by submerging them in a cleaning solution. High-frequency sound waves create microscopic bubbles that remove impurities from complex mold surfaces. Since ultrasonic cleaning is non-invasive, it guarantees complete cleanliness, which improves mold function and lengthens its lifespan.
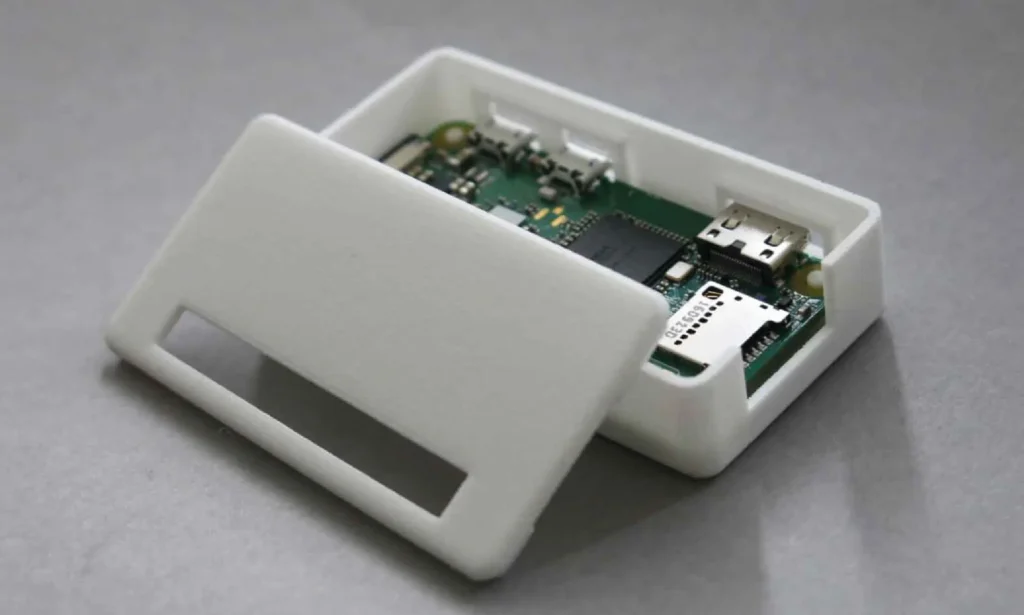
Injection Molds: Ultrasonic cleaners carefully clean molds used in plastic injection molding, ensuring accurate product reproduction and minimizing flaws.
- Traditional Cleaning – Disassembling molds, manually scrubbing each component with brushes and solvents, and inspecting and reassembling the parts for reuse.
Extrusion Dies: Extrusion die cleaning eliminates residue buildup, ensuring correct extrusion profiles and product uniformity.
- Traditional Cleaning – Disassembling the dies, manually scrubbing components with brushes, solvents, and abrasives, and inspecting for residue removal.
Plastic Parts: Companies clean electronic housings and medical devices, for example, to remove manufacturing residues and ensure correct function.
- Traditional Cleaning – This includes using brushes, towels, or compressed air to scrub or wipe, cleaning solutions, and water rinsing.
Additive Manufacturing: Ultrasonic cleaning aids in the cleaning of 3D-printed plastic parts by eliminating support material and improving surface smoothness.
- Traditional Cleaning – Inspect components visually, then apply solvents using brushes or cloth for scrubbing. Occasionally, use abrasive materials for stubborn contaminants, but be cautious of potential damage to the plastic.
Blending and Mixing Equipment: Cleaning mixing equipment eliminates cross-contamination and ensures that plastic compositions are consistent.
- Traditional Cleaning – Operators would dismantle the equipment, manually scrub each part with brushes and solvents, rinse thoroughly, and then reassemble.
Overview of Contaminants Affecting Plastic Components: Causes, Effects, and Solutions
Industrial ultrasonic cleaners are essential to the plastic industry’s ability to uphold strict cleanliness regulations. These cleaners remove impurities from equipment surfaces, molds, and recycled materials, including leftover monomers, processing additives, and lubricants, using high-frequency sound waves. Ultrasonic cleaners help avoid cross-contamination by providing thorough cleaning and reaching difficult-to-reach locations. This ensures that different materials treated with the same equipment do not degrade the quality of the final plastic goods. Furthermore, their effectiveness in surface preparation and drying improves the entire production process, which helps to ensure the consistent and dependable production of high-quality plastic components.
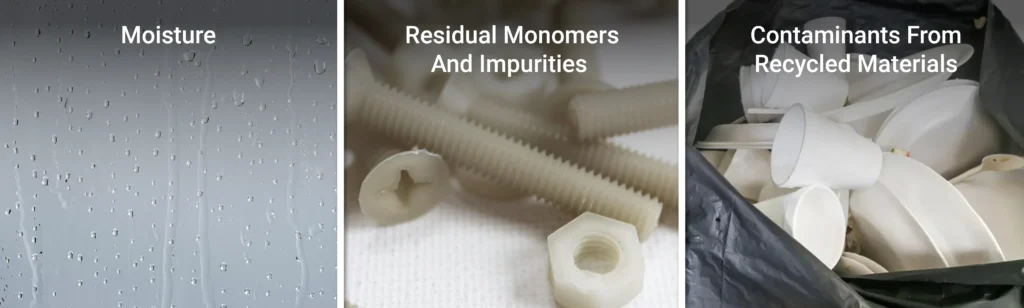
Moisture
- Causes: Improper storage conditions, ambient air, and raw ingredients may all bring moisture into the plastic manufacturing process.
- Effects: Moisture can affect the mechanical and physical qualities of plastics, leading to flaws such as bubbles, blisters, or uneven surface finishes.
- Solutions: Properly drying raw materials, maintaining low humidity in processing facilities, and using moisture-resistant packaging can help avoid moisture contamination.
Residual monomers and impurities
- Causes: Remaining monomers or contaminants may be present during manufacture as a result of incomplete polymerization processes.
- Effects: Residual monomers and contaminants can impact the mechanical qualities, stability, and color of plastic. They might also be a factor in environmental and health issues.
- Solutions: Strict quality control procedures, effective purification techniques, and adherence to the right polymerization conditions actively reduce the amount of residual monomers and contaminants.
Contaminants from recycled materials
- Causes: Recycled materials could have dirt, incompatible plastics, food residue, or other impurities from their prior use.
- Effects: Recycled materials may have contaminants that affect the new plastic products’ qualities and characteristics.
- Solutions: Achieving a reduction in pollutants involves implementing efficient recycling procedures, thoroughly cleaning recycled materials, and using appropriate materials in recycling streams.
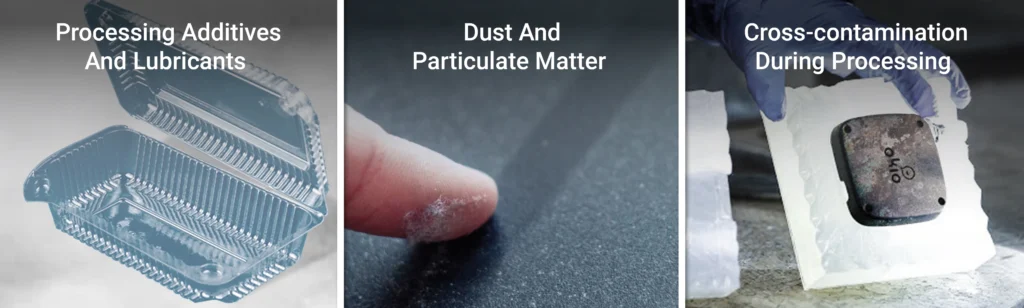
Processing additives and lubricants
- Causes: The finished product may contain leftovers from lubricants and additives employed throughout the production process.
- Effects: Remaining processing additives may have an impact on the plastic’s performance and cause problems like poor adhesion, weakened structure, or surface imperfections.
- Solutions: Opt for additives with low volatility, use appropriate processing conditions, and implement effective cleaning processes to remove residues.
Dust and particulate matter
- Causes: Particulate particles and dust in the air may enter the production process from outside sources.
- Effects: Dust contamination can affect the overall quality, cause surface defects, and lessen the transparency of the product.
- Solutions: Implementing effective dust control methods, maintaining clean manufacturing facilities, and using suitable filtering systems can all help to reduce dust contamination.
Cross-contamination during processing
- Causes: When various materials are treated on the same piece of equipment without being properly cleaned, cross-contamination can happen.
- Effects: Combining materials that aren’t compatible can result in faulty products, decreased functionality, or even safety issues.
- Solutions: Use specialized equipment for different materials, follow stringent cleaning processes, and provide explicit procedures for switching out materials.
Advantages of Using Industrial Ultrasonic Cleaners in the Plastic Industry
- Versatility – Glass, metal, plastic, ceramic, and other materials can all be cleaned using ultrasonic cleaning because of its versatility. It can be adjusted to various parts and machinery utilized in the plastics business because of its adaptability.
- Reduced Labor and Time Requirements – The cleaning process can be automated by ultrasonic cleaners, negating the need for labor-intensive scrubbing or equipment disassembly. This considerably cuts down on the amount of time needed for cleaning operations in addition to labor savings.
- Improved Efficiency in Production Processes – Ultrasonic cleaners help to increase industrial operations’ overall efficiency by keeping tools and molds clean. Maintaining clean equipment minimizes downtime and boosts production by lowering the chance of faults and ensuring consistent product quality.
- Drying Capabilities – Certain ultrasonic cleaners have drying functions built in, enabling a thorough cleaning and drying cycle. This is advantageous since properly dried components are ready for use right away, reducing moisture-related problems in the plastic production process.
- Environmentally Friendly – Ultrasonic cleaning is a more environmentally friendly alternative because it typically only needs a light cleaning solution, as opposed to certain standard cleaning procedures that may entail harsh chemicals.
In conclusion, industrial ultrasonic cleaners have many benefits that greatly improve the general efficiency, quality, and cleanliness of production operations. Their high level of cleanliness is guaranteed by their capacity to remove impurities from molds, recycled materials, and equipment while also providing precise cleaning in difficult-to-reach places. Ultrasonic cleaners are essential for optimizing processes and boosting output since they cut down on labor and time needs, avoid cross-contamination, and improve the quality of recycled materials. By implementing these technologies, the plastic industry not only produces dependable and predictable outcomes, but also shows that it is committed to environmental sustainability by using fewer harsh cleaning agents. In the end, industrial ultrasonic cleaners are indispensable instruments that support a more ecologically friendly, productive, and hygienic method of producing plastics.
For other Sonixtek news and updates, follow the Sonixtek Facebook Page.